Packaging
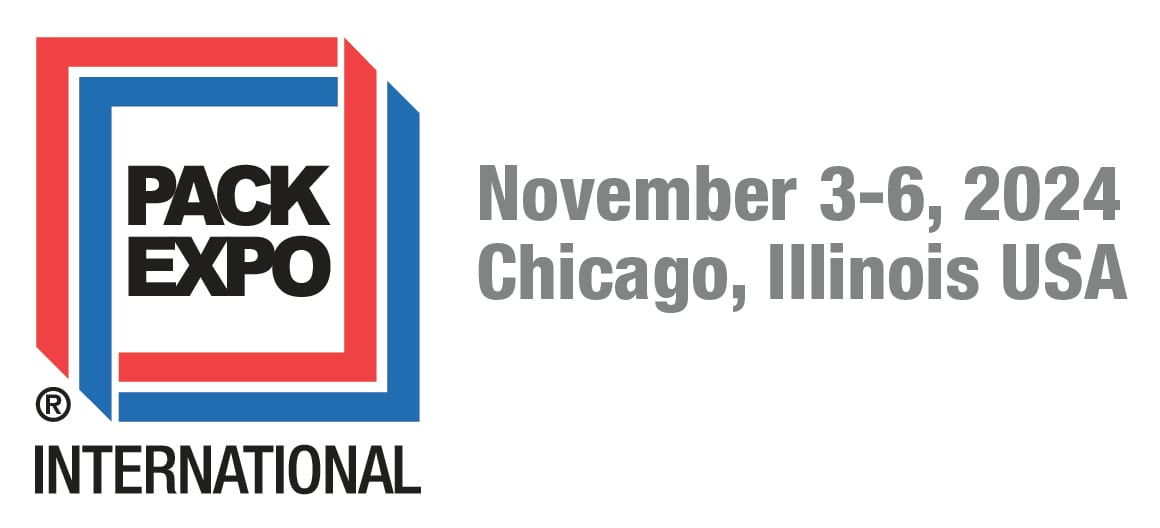
PACK EXPO International sees record number of exhibitors
Packaging, processing companies highlight solutions that can support beverage operations
(Image courtesy of Chinnapong/iStock / Getty Images Plus via Getty Images)
PACK EXPO International, which took place Nov. 3-6, wrapped up its four-day stint at McCormick Place in Chicago. Produced by PMMI, The Association for Packaging and Processing Technologies, the show brought together 48,000 attendees and 29,500 exhibitor personnel, reaching 77,500 in total attendance. International attendance increased 19% compared with 2022.
A record number of 2,700 exhibitors occupied 1.32 million net square feet of space, making PACK EXPO International the largest show in its history and the biggest event at McCormick Place this year.
“PACK EXPO International 2024 has truly raised the bar for what an industry event can achieve,” said Jim Pittas, president and CEO at PMMI, in a statement. “This show has not only grown in scale but also in substance, attracting attendees and exhibitors from every corner of the industry. The connections made here are invaluable, reinforcing PACK EXPO’s role as an unmatched platform for innovation, collaboration, and progress across the packaging and processing landscape.”
The show has grown significantly year over year with a 10% increase in exhibit space and a 24% increase in the number of exhibitors from PACK EXPO International 2022.
“All across the board, our numbers have increased. Exhibitors continue to showcase top innovations, and attendees are flocking to see the latest solutions to their manufacturing challenges,” said Laura Thompson, vice president of trade shows at PMMI. “It’s not just the size of our show which draws people in ― it’s the quality.”
With seven pavilions tailored to meet industry demands, new show features like Sustainability Central and Emerging Brands Central, and show resources to help attendees plan their days, attendees found value throughout the show.
The following are some of the exhibitors at the show that serve the beverage market:
Admix Inc. highlighted its hygienic and industrial process industries, providing cutting-edge mixing, blending, dispersing, and milling solutions. The Admix Fastfeed system is an inline powder induction and dispersion system designed to tackle the most demanding batching challenges, the company says. The Fastfeed system is a fully integrated solution that features a two-stage rotor/stator high-speed disperser coupled with a powerful powder suction pump. The company also offers its Dynashear Inline Mixer, the Boston Shearmill wet mill/homogenizer and the Rotosolver High Shear Mixer.
Columbia Machine manufactures inline high speed, high level, floor level, robotic hybrid palletizers, load transfer stations and provides complete system integration. The new FLD2500-SW palletizer is the latest design from Columbia Machine. With the same standard safety content and superior package handling flexibility like all Columbia conventional palletizers, the FLD2500-SW has an extremely compact footprint and simultaneously stacks and stretch-wraps a variety of package types including cases, trays, shrink bundles, display packs and more, it says.
Delkor Systems Inc. highlighted its advanced robotic packaging systems for the food, beverage and consumer products industries. The company featured live demos of its EVO Case Packer, LSP Series Case Packer and Trayfecta X Series Former. Delkor’s Trayfecta X Series corrugated case former features
Delkor’s patent-pending corrugated warp correction technology, can handle 50 cases a minute with 500 blank magazine capacity and offers three-minute changeover between all shipper styles, including club store stackable trays, it notes.
GEA announced that a state-of-the-art testing will be opening in Janesville, Wis., in 2025. The company also promoted its SmartPacker portfolio and the GEA Unibloc Flex. The Unibloc Flex is a line system for filling aluminum bottles with aseptic processing technology. The GEA Unibloc Flex can process extremely sensitive liquid products, including milk-based and plant-based beverages, either still or carbonated, with or without particles.
Klüber Lubrication highlighted its high-performance specialty lubricants. The company provides food-grade solution to eliminate all challenges that reduce efficiency. For blower machine and packing, Klüberfluid NH1 CM 4-100 Spray has a fully synthetic hydrocarbon oil base combined with a carefully selected, high performance solid lubricant and additive package. It was designed without mineral oil in order to minimize the risk of MOSH/MOAH contamination. When applied correctly, a semi-dry lubricating effect can be attained. For bottle washing machines, Klüberfood NH1 94-402 is a special lubricating grease composed of a highly refined base oil and a calcium complex thickener. The use of Klüberfood NH1 94-402 can contribute to a safe product regime when used in accordance with food manufacturing regulations. For filling machines, PARALIQ GTE 703 is a special lubricating grease based on silicone oil and PTFE, designed for very low-load rolling bearings used in the beverage industry where an EPDM-compatible H1 lubricant is required. For conveyor systems, Klüberplus C2 PM2 Ultra Dry is a homogeneous solution where the soluble raw materials do not get separated. This helps to prevent deposits (residues) on conveyor belts and considerably reduces the risk of nozzles getting blocked.
Krones promoted its aseptic systems family, which included experts for all kinds of different sterilization methods and products to be filled, including the Contipure AseptBloc. Regardless of whether its blow molding, filling or capping, the Contipure AseptBloc supports every production step is handled safely in an aseptic processing chain, it says.
Lasnek Ltd. promoted its stainless steel cable management products. With more than 30 years of engineering expertise in stainless steel fabrication, Lasnek has demonstrated its commitment to quality, service and technical innovation by supplying manufacturing, installation and production companies high quality solutions and components, it says.
PDC International Corp. promoted its shrink sleeve labeling, tamper evident neck banding and shrink tunnel technology. The company showcased the R-250 Evolution, a next generation sleever utilizing new design and construction methods. The machine can apply oriented graphics onto non-round containers such as ovals and squares, in addition to round containers. The R-250 brings high speeds and durability with a reduced footprint and superior value, the company says.
ProMach Brands featured a variety of its divisions, including Serpa, which displayed the FG1 Top Load Carton/Tray/Case Former. This machine is the ultimate all-in-one option for customers needing a high level of flexibility, it notes. Serpa also brought five other machines: the P100 Horizontal Continuous Motion Cartoner, P200 Side Load Case Packer, TEL10 Tamper Evident Labeler, RF450/TL450 High Speed Insert Feeding and Tray Unloading System and FM150 Intermittent Motion Beverage Cartoner. Texwrap also introduced the newly updated DX-130 Dual Roll Bundler to PACK EXPO this year, demonstrating its size and speed capabilities that go beyond its small footprint. Also on hand was the Kayat SRX Series, a flexible platform for customers looking for a single roll bundler in the food and beverage industry. Attendants also saw the SRX-CUF bundling loose items, a growing trend in packaging. The OSS-145 Continuous Motion Orbital Side Sealer rounds out the Texwrap booth with its simplicity and ease of use.
Ryson International Inc. promoted its spiral conveyors. Ryson spiral conveyors need less floor space than conventional incline conveyors and are faster and more reliable than any elevator or lift, the company says. They are especially well suited for consumer packaged goods companies and any warehousing operations, it notes. The company’s mass flow spirals handle full and empty bottles, cans and jars in mass up to 2,000 units a minute, and are available in four different slat widths ranging from 6 to 20 inches.
SOMIC Packaging Inc. showcased its 434 next generation case packing system. This high quality and versatile modular machine is based on fixed function groups consisting of proven, tested, and standardized mechatronic systems, the company notes. The 434 is designed to handle up to 34 cases a minute during a single cycle, format adjustments are 70% faster than previous systems, it says. The 434 includes new frame construction for improved ergonomics, noise reducing features, and a QuickChange adjustment system for faster and easier format changeovers, the company notes. Additionally, the Twin Cities area packaging manufacturer of automated, mechatronic retail ready machines shared its recently completed purchase and renovation of a 48,000 square-foot building at the InverPoint Business Park in Inver Grove Heights, Minn. In addition to now having the ability to assemble all new North American machines and with room for future growth, the move retains accessibility to several major highways and close proximity to nearby Minneapolis International Airport.
Standard-Knapp Inc. celebrated its 130th anniversary by showcasing four machines at the show: Robotic palletizer from A+F Automation (Kirchlengern, Germany); FlexLine delta robot packer, also built by A+F; Unipack 2.0 pick-and-place case packer from BMS (Pfatter, Germany); High-speed servo laner from Standard-Knapp (Portland, Conn.); and Conveyor system from NEO Conveying Intelligence (Porto, Portugal). Pack Expo International also marked the first demonstration of a palletizer or FlexLine by Standard-Knapp, as well as its new custom conveyor systems, and the Chicago debut of the company’s fully updated booth display.
Teledyne Taptone promoted its X-ray senor Fill xr for fill level inspection. The Fill xr sensor is a non-contact sensor used to measure the product fill level in steel, aluminum, glass, plastic and paper containers. An x-ray tube energized at high voltage is used to produce a low energy x-ray beam. This x-ray beam is focused to look through the container in the expected fill level region. The TapTone Fill xr sensor uses low energy X-ray technology to inspect steel, aluminum, plastic and glass containers for proper fill level. The system can be configured to detect underfilled and overfilled containers. The sensor mounts on a remote variable height stand and requires no modifications to the existing production conveyor. The Fill xr sensor can be added to existing TapTone systems as an optional inspection.
Thermo Fisher Scientific promoted product inspection and analytical instrument solutions for food, pharmaceutical, and consumer products. Its X-ray inspection systems provide protection from metal, glass, stone, and other dense foreign objects. Models range from its entry-level Thermo Scientific NextGuard X-ray system to its high-performance, flexible Thermo Scientific Xpert systems. Thermo Scientific FTIR instruments and handheld XRF analyzers help identify the makeup of debris found in food, enabling food processors to more quickly identify the source and resolve contamination issues, it notes.
Vacuum Barrier Corp. demonstrated its newest high-speed liquid nitrogen dosing system. The company displayed its NITRODOSE G3 SERVODOSER, whose differentiators include the ability to adjust the flow rate during discrete and continuous dispensing without changing nozzles. An advanced dosing system designed for fast, precise delivery of low-pressure liquid nitrogen in beverage applications, the NITRODOSE G3 SERVODOSER allows manufacturers to adapt to their production needs without downtime, the company says. The seamlessly integrated system can handle up to 2,000 containers per minute (CPM) while offering exemplary dosing control, it notes. The NITRODOSE system is used for non-carbonated beverages in plastic bottles or aluminum cans, where it adds rigidity to enhance structural integrity and durability. Equipped with a 7-inch color touchscreen for intuitive operation, the NITRODOSE G3 SERVODOSER can deliver dosing durations as brief as 4 milliseconds and offers an accuracy of approximately plus or minus 1% of dose weight, according to the company.
Videojet Technologies showcased its latest product innovations designed to enhance manufacturers packaging operations. New in 2024 and recently enhanced with the capability to manage up to four printheads with a single controller, Videojet released the 2380 LCM printer, which can print on multiple sides of cases and cartons. Its direct-to-box printing functionality reduces pre-printed case and carton inventories to decrease costs, storage needs and waste, while allowing for quick changes in print content. A complete large character marking system, the 2380 LCM prints durable high-resolution text, logos and bar codes on cases and cartons, meeting the demands of the distribution chain. New at Pack Expo, Videojet 9560 PL pallet labeler is a reliable automated pallet labeling system that helps reduce warehouse costs and mistakes, the company says. Specifically engineered to function in demanding conditions, the 9560 PL can cover two or three sides with up to four labels, processing up to 120 pallets an hour across a range of applications, it notes.
The next PACK EXPO event is the brand-new PACK EXPO Southeast, which is scheduled for March 10-12, 2025, at Georgia World Congress Center in Atlanta.