Supplier’s Marketplace
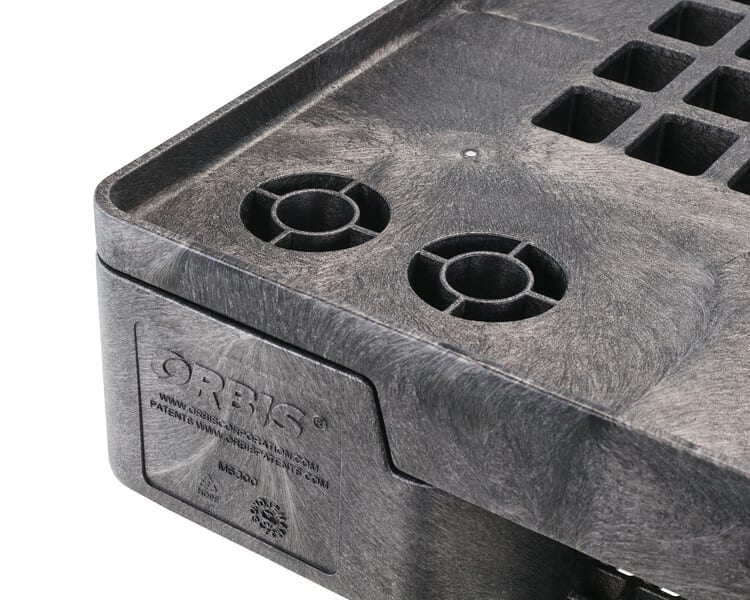
ORBIs
1055 Corporate Center Drive, Oconomowoc, Wis. 53066; 800890-7292; www.orbiscorporation.com
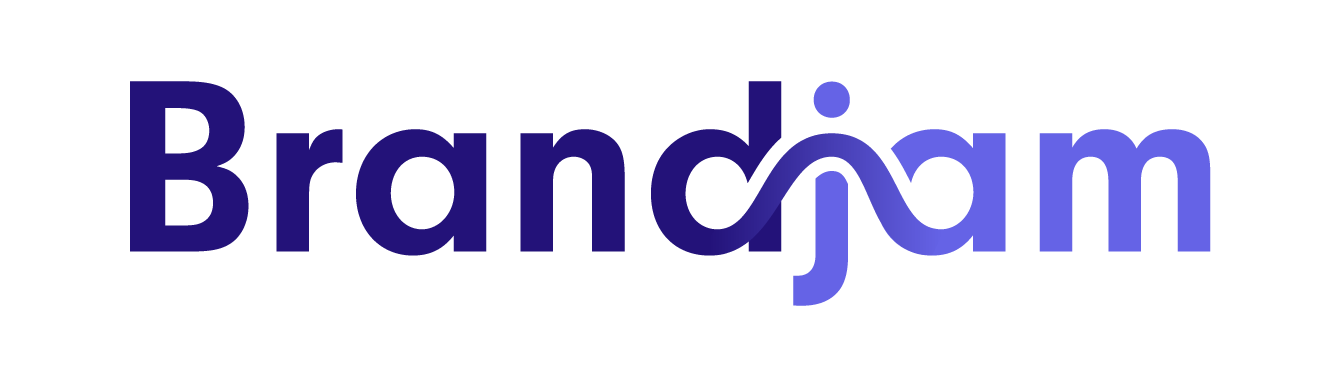
Brandjam
2110 Bardstown Road, Unit B, Louisville, Ky. 40205; 502/384-6331; www.brandjam.com
ORBIS introduces new industrial pallet
Reusable packaging solutions provider ORBIS Corp. announced its latest innovation in sustainable packaging materials. The company unveiled a 60-by-48 industrial pallet specially designed to cater to the unique requirements of EV and powertrain applications. The new pallet is manufactured through a process of structural foam injection, boasting exceptional durability and reliability. These qualities make it an optimal choice for use within the industrial and automotive sectors, the company says. The pallet is well-suited for transporting powertrain and EV components like modules and longer battery components. It offers compatibility with automation and edge-racking systems that enhance operational efficiency and versatility in handling and storage. “We’re so excited to introduce our new 60x48, as this reinforces our ongoing commitment to provide reliable and durable solutions for the EV and powertrain industries,” said Bre Herbert, senior product manager, in a statement. “With this new product, we’re able to offer enhanced load security and efficiency in handling and transportation.” The design of the pallet enables edge racking capability and the option to incorporate metal reinforcements for added strength, ORBIS notes. The company also offers a thermoform topcap to secure unit loads.
Brandjam delivers first-party data solutions
Data solutions provider for the beverage industry, Brandjam, is designing and building a “data distillery.” The “distillery” aims to advance the industry by connecting brands to their end consumers. Brandjam’s mission is to revolutionize how distilleries, visitor centers and alcohol brands leverage consumer data. It delivers cutting-edge tools that provide unparalleled insights into consumer behavior and preferences. Because consumer data is the “key to unlocking business growth,” Brandjam says it enables beverage alcohol brands to capitalize on the power of first-party data. The company has transformed the consumer experience at distilleries and live events thanks to its experiential data capture technologies. The technologies include interactive self-serve kiosks and automated, post-visit engagement capabilities. The seamless integration of data capture tools allow brands real-time access to personalized insights into consumers preferences, purchasing habits and product affinities, the company explains. Its data system provides brands with a clear picture of their consumers, allowing for highly targeted, one-on-one marketing. This enables brands to personalize consumer marketing strategies and boost direct-to-consumer (DTC) sales, it says. “Our platform makes first-party data not only accessible, but actionable,” said Tom Cottingham, CEO, in a statement. “Beverage alcohol brands can now gather crucial data from the moment a consumer enters a venue, turning that information into a competitive advantage. With our technology, these brands can finally see their consumers clearly, which drives better marketing, sales and long-term growth.”
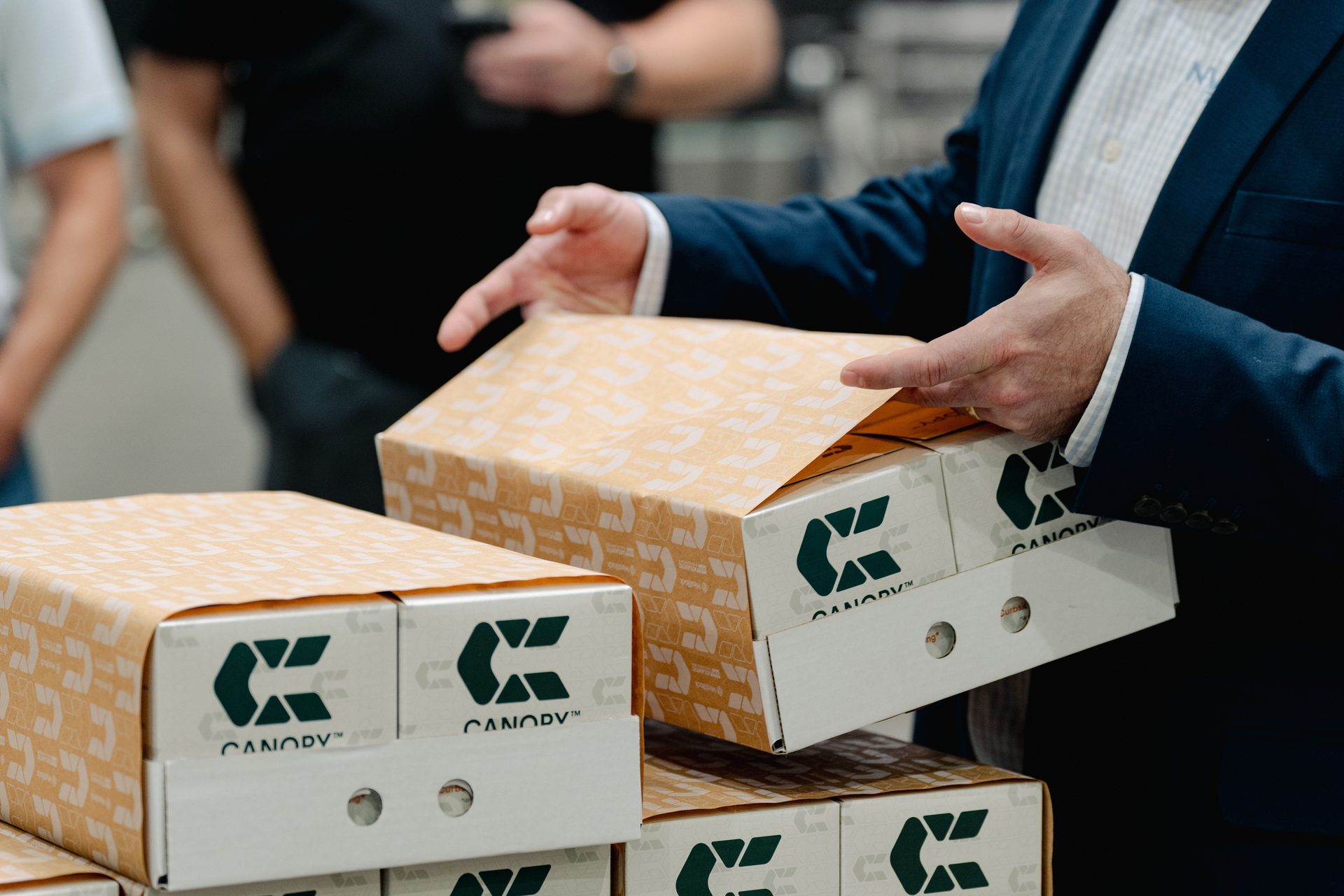
Atlantic Packaging
3444 Baker Road Northwest, Suite 200, Acworth, Ga. 30101; 770/422-8800; www.atlanticpkg.com
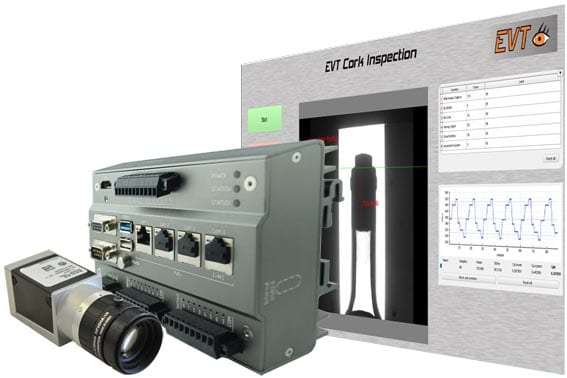
Eye Vision Technology
Ettlinger Strasse 59, 76137 Karlsruhe, Germany; +49 (0) 721-668-004-230; www.evt-web.com
Atlantic Packaging launches new Canopy Wrap systems
Privately owned industrial packaging company Atlantic Packaging recently announced a newly designed Canopy Wrap system. The system is a solution for fully curbside recyclable bundling applications, replacing traditional shrink film and running on nVenia equipment. It utilizes paper from Smurfit Westock. The wrap delivers a competitive offering to customers seeking to prioritize sustainability without compromising performance and efficiency through a tested fiber wrap material and high-speed application process, the company says. “Atlantic Packaging is excited to deliver the new Canopy Wrap system as part of our larger, ongoing efforts to help the supply chain transition away from single-use plastics,” said Wes Carter, Atlantic Packaging president, in a statement. “When it comes to shrink bundling for bottles, cans and food products, the shrink film is typically the only component preventing full curbside recyclability. Canopy Wrap helps overcome this barrier, making it easier for companies to meet their sustainability goals as we collectively work together to implement sustainable packaging solutions for a healthy planet.” Atlantic Packaging, with equipment from nVenia, delivers a high-speed, automated solution for application as fast as 30 bundles a minute, it says. The equipment solutions from the company also are available as a retrofit to existing bundling machinery or as a dedicated high-speed bundler. “We are proud to partner with Atlantic on this solution as ongoing pressure of new legislation, consumer demand and priorities in the c-suite to reduce waste and create sustainable packaging continues to drive more environmentally focused purchasing decisions,” said Paul Ferrandino, nVenia senior vice president of sales, in a statement. “We look forward to helping customers achieve their sustainability goals while helping set a new industry standard with Canopy Wrap.”
EVT’s EyeVision, EyeBundles assist in precision
Because precise and reliable inspections are essential for quality assurance in the beverage industry, EVT’s EyeVision software allows users to achieve these goals, it says. The software provides detailed and highly accurate inspections at every point in the bottling process, the company notes. Users can perform all the necessary inspections with one tool when using EyeVision, it adds. EVT offers EyeBundles for those looking for a complete solution, with ready-to-use systems tailored to specific tasks, combining EyeVision software with the required hardware. The software’s inspection tools cover all areas, the company says, ensuring bottles leave the production line in perfect condition. The software features cap verification that confirms each cap is sealed, aligned and color-matched, as well as a label inspection to ensure correct label position, orientation and color. It also has neck and thread analysis, which detects chips, cracks and thread wear on the bottle neck, as well as fill level control. The control monitors each bottle’s fill level and flags overfills or underfills. EyeVision’s EyeBundles provide ready-to-us systems tailored for specific inspection needs, it notes. The bundle combines EyeVision’s adaptable software with a hardware setup, ready to tackle specific tasks and easily adjustable to production demands.
Toyota Material Handling unveiled an upgrade to its parts distribution center at its Columbus, Ind. headquarters. The upgrade was in collaboration with Bastian Solutions, which is part of Toyota Automated Logistics. “At Toyota, we will always be driven by what is best for our customers,” said Bret Bruin, vice president of aftermarket operations at Toyota Material Handling, in a statement. “It’s amazing to see this project come together, in partnership with the teams at Bastian and AutoStore, to eliminate unnecessary waste and add efficiencies for the benefit of our customers.” The upgrade marked Bastian’s 100th AutoStore system installation.
Mitsubishi Logisnext Americas Inc. (Logisnext) reaffirmed its commitment to “Moving the World Forward” by donating two motorized Mitsubishi Forklift pallet trucks to the Houston Food Bank (HFB). The food bank is one of the largest in the nation and plays a critical role in distributing food in need to those across southeast Texas. “We are deeply committed to supporting the Houston Food Bank in their mission to combat hunger in our community,” said Ken Barina, president of Logisnext, in a statement. “By providing these electric pallet trucks, we aim to enhance their ability to distribute food more efficiently, ensuring that more families in need receive the help they deserve. It’s an honor to contribute to such a vital cause and the Houston Food Bank in their efforts to make a positive impact in Great Houston.”
Mengniu was recently awarded “lighthouse factory” certification by the World Economic Forum (WEF) for its world-first, fully intelligent factory in Ningxia, China. The site was recognized for its innovation, as it uses Tetra Pak’s end-to-end solutions with a network of specialists and partners. The factory was co-designed by Tetra Pak and Mengniu, utilizing Tetra Pak’s digital platform and state-of-the-art production equipment. Digital systems control the entire processing and packaging process, monitoring performance in real time and automatically routing to the most suitable equipment, the company explains.
Logistics automation innovator Cimcorp appointed Pekka Natri to head of region for North America. He has been a key member of the company since 2018 and now will be responsible for streamlining all North American operations. “I am thrilled to take on this new opportunity to strengthen Cimcorp’s position as a leader in the North American market,” Natri said in a statement. “As head of region, my goal is to make an immediate, positive impact for customers and employees today, as well as to set the groundwork for ultimately shaping the future of automation in our core sectors — grocery retail and tire manufacturing.”
Gravity flow solutions provider Mallard Manufacturing announced the appointment of Brian Meyer as national accounts manager. Meyer has more than 30 years of experience in the material handling industry and has held pivotal roles in manufacturing and integrator/dealer sectors. “At Mallard Manufacturing, I see an unparalleled commitment to customer-focused support and innovation,” Meyer said in a statement. “The new Innovation Lab and Testing Center exemplifies our dedication to ensuring our solutions not only meet, but exceed, consumer expectations. This facility allows us to conduct comprehensive live-feed and interactive simulation testing, addressing potential challenges before finalizing pallet flow and carton flow solutions.”