Operations
On the move
Conveyor systems aid beverage-makers in wake of shifting consumer preferences
By Chloe Alverson
(Image courtesy of Dematic)
Kelly Clarkson’s 2011 song “Stronger” is all about self-empowerment after a relationship ends. “What doesn’t kill you makes you stronger / Stand a little taller / Doesn’t mean I’m lonely when I’m alone,” she sings in the chorus.
In the beverage industry, consumer trends are making the conveyor systems market stronger, experts share.
Gary Proffitt, applications and engineering manager at Sentry Equipment, Oconomowoc, Wis., says the conveyors market remains strong.
“Growing consumer demand in all markets drive customers to expand their production capabilities,” he shares. “They require more conveyor and equipment to keep up and more frequently replace items that are inadequate or a source of downtime. The equipment must be user friendly, robust and capable of higher speeds.”
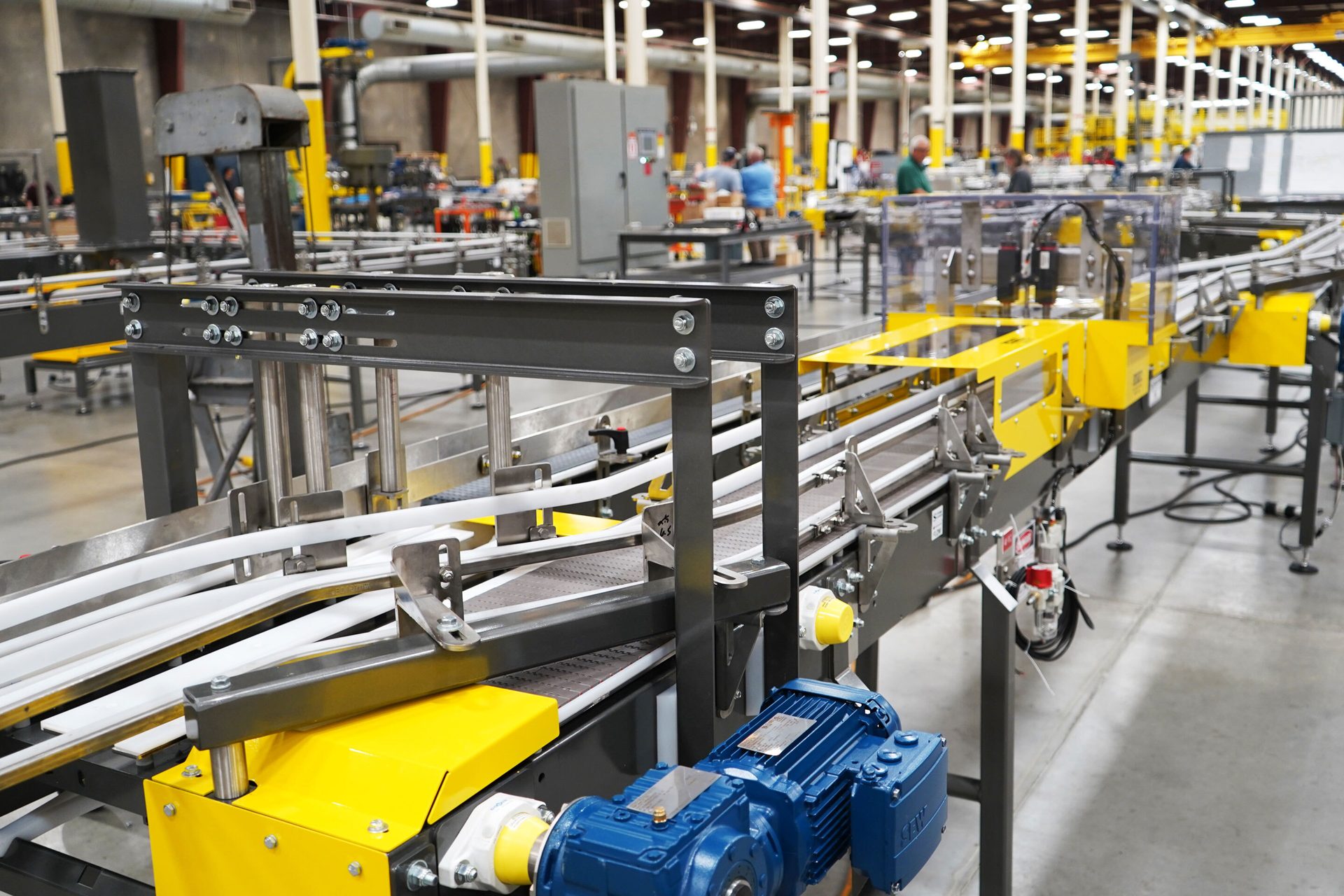
Today’s conveyor systems must be designed to handle a wide variety of beverage products, Sentry’s Proffitt shares.
(Image courtesy of Sentry Equipment)
Safety and production efficiency are paramount, Proffitt adds, so beverage-makers demand conveyors that are designed and built to meet those needs.
Similarly, Brandon Duba, solution consultant at Atlanta-based Dematic, notes that, while the broader market is evolving, the conveyor market is seeing steady growth.
“This is driven by increased volume and SKUs in warehouses and production facilities,” he explains. “Beverage-makers are shifting their portfolios to meet changing consumer tastes. Demand for conveyors is also rising due to multi-channel delivery models like eCommerce and direct-to-consumer (DTC), which require more complex automation.”
Conveyors are essential to connecting and powering these systems, Duba adds. The proliferation of beverage packaging formats is impacting the conveyor market as well.
“As beverage packaging evolves, conveyors must remain agile,” Duba says. “Customization is essential, with systems adjusting speed, orientation and alignment to match production needs. Customer-facing packaging requires careful handling to prevent damage.”
Varying shapes and sizes demand advanced sensors and tracking, he states.
“Flexible pouches, in particular, pose unique challenges, often requiring pocketed belts or v-groove conveyors due to their lack of rigidity,” Duba explains. “Their instability and lightweight design make controlled speed critical.”
Sentry’s Proffitt explains that beverage companies consistently look for new ways to market their products, resulting in unique packaging formats and configurations.
“Conveyors need to handle a wider range of products on the same system,” he says. “Customers expect minimal downtime and want these systems to be more automated for ease of operation and a fast changeover. Smaller, lightweight containers and flexible packaging lead conveyor manufacturers to design equipment in a manner that eliminates product damage and reduces operator intervention.”
New products also promote the use of robotics in lieu of previous, conventional technology for handling and packaging, Proffitt shares.
Other trends are affecting conveyor systems. Dematic’s Duba points to automation investments, which he says heavily influence conveyor systems.
“Producers and distributors demand speed and accuracy across the supply chain, and conveyors are key to managing increased throughput and linking advanced technologies,” he says. “They reduce human intervention and control movement from pick modules to buffer systems and palletization. While speed and accuracy are critical, sustainability is also a focus.”
Beverage operations also continue using conveyors to cut waste and lower energy use, Duba notes. Sentry’s Proffitt shares comparable thoughts regarding an increased focus on sustainability.
“The impact that packaging methods ultimately have on the environment has been realized more in recent years and both manufacturers and consumers are looking for ways [to] mitigate that as well as support other companies that do the same,” Proffitt says. “Another trend in the food and beverage industry is the search for healthier product options. New products often lead to the need for different packaging and dedicated equipment to support it.”
“Consumers tend to fall back on bottled waters for their perceived safety and better taste compared to tap water. Safety, health and convenience perks will drive continued growth of bottled waters.”
– Julia Mills, food and drink analyst at Mintel
“Demand for conveyors is also rising due to multi-channel delivery models like eCommerce and direct-to-consumer (DTC), which require more complex automation.”
– Brandon Duba, solution consultant at Dematic
Considering conveyor systems
Some requests from beverage manufacturers and distributors are more common than others when it comes to conveyor solutions.
Beverage distributors are seeking innovative ways to handle a growing variety of packaging, Dematic’s Duba says.
“As packages become smaller and more flexible, specialized material handling solutions are required,” he shares. “These systems must also minimize floor space, as warehouse real estate is at a premium. Reducing the footprint can lead to major savings or cost avoidance.”
Distributors also prioritize maintainable solutions with a low cost of ownership, Duba notes.
Sentry’s Proffitt says that some of the highest priorities for manufacturers are safety, ease of maintenance and ease of changeover when handling multiple product sizes, high-speed capabilities, fast delivery and good customer service.
“Safety is, and should be, the focus for almost any business,” Proffitt states. “No injuries is the goal for any employer and equipment that is designed with that in mind is recognized and has increased value.”
Customers require more output from their equipment and cannot afford downtime or missed production, he adds.
“When they do encounter challenges, they expect fast solutions and support from their vendors,” Proffitt says. “With so many equipment manufacturers to choose from service can often be the aspect that separates one from another.”
He also shares thoughts on how artificial intelligence (AI) could influence conveyor equipment.
“Artificial intelligence could help many companies identify areas of inefficiency and ways to improve upon them,” Proffitt states. “AI may provide data and the ability to analyze in ways other systems cannot. It could also play a significant role with customers who need to handle and implement complex sorting of products in large warehouse systems.”
AI is set to rapidly advance conveyor technology, Dematic’s Duba anticipates.
“AI will adjust conveyor settings to accommodate different packaging types with minimal maintenance and fewer errors,” he says. “Data-driven decisions will enable smarter, more dynamic routing with improved prioritization. This marks a major step forward in wave-less routing, boosting throughput and reducing the need for buffer space.”
As for what the future holds for conveyor systems, Duba suspects they will evolve alongside material advancements.
“Belts will become stronger and lighter, sensors smarter and materials more sustainable — boosting energy efficiency,” he shares. “As packaging shifts to more eco-friendly formats, conveyor solutions will grow more flexible, allowing quick adjustments with minimal downtime between runs. Communication between systems will also improve, with real-time data sharing enhancing capacity and reducing bottlenecks as conveyors respond to signals from other automation.”
Meanwhile, Sentry’s Proffitt shares that, with increased demand from customers, the design and functionality of equipment must constantly evolve.
“Manufacturers will always look for ways to promote safety, automate systems, increase output, reduce labor costs and focus on sustainability,” he concludes. “Equipment providers that are able to separate themselves by offering cost-effective solutions to meet those needs will see the most success. Ultimately, solutions that allow customers to increase their production with reduced costs and downtime hold the most value.”